I've been thinking about helve hammers after looking at those photos from the Italian coach building shops from years ago. I stubbled across this build that Tom Lipton did and documented on his blog several years ago.
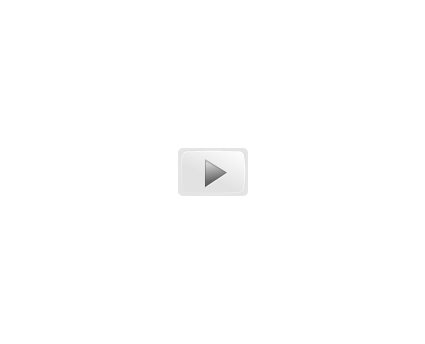
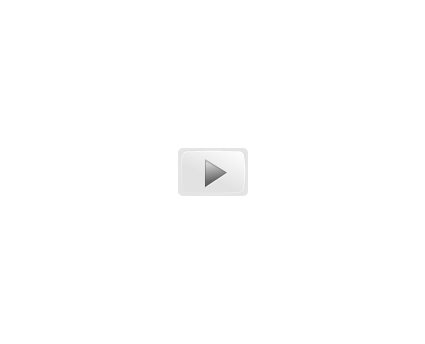
It was around 1999 when I took a trip out to visit my friend Wray Schlelin out in Massachusetts that I started forming the ideas for my Helve Power hammer. Wray had built a Helve hammer quite a few years before that to support his home based metalshaping business. He builds replacement sheetmetal parts for old Jaguar 120's and 150's. His customers are high end restoration shops and avid Jaguar club members that are rebuilding their rotted out barn finds. He supports his family from this work alone. I met Wray over the internet. I can't quite remember the situation but I think it all started with a article he did for Artmetal on the art related uses for the English wheel and some of his innovative tools and equipment.
Wray got part of his inspiration for a Helve hammer from a tiny little picture he found in a magazine or book. I'm pretty sure this is the picture below that got him started building his own helve hammer.
This is the helve hammer Wray built with only a tiny picture and some motivation. His hammer has been used regularly for something like twenty years or more. A testament to its construction. Its amazingly quiet. You can easily carry out a conversation standing next to the operator. Not much of a picture to go on but it was enough. Below is a video of Wray's hammer in action.
The origin of the Helve hammer goes back to ancient Chinese and Roman times. There are drawings of water powered trip hammers that are basically a Helve powered by a water wheel or bunch of young indentured apprentices. Helve means handle or shaft much like the handle on a normal hammer or an axe handle. They swing in an arc like the natural swing of a human but with a lot more endurance. This distinguishes Helves from other types of power hammers like Little Giants (below) and big Yoder type hammers which are both called guided way hammers.This means they can have both top and bottom dies that meet in a precision way to perform special work.
There are two distinct end uses that determine the construction and accessories for Helve type of power hammers. One is forging like you would see a blacksmith do where the metal is heated and worked red hot. The second type is the type I was interested in building which is for compound sheet metal shaping.The work material is much thinner and the material is worked cold.
Above is a picture of a monster Yoder hammer, probably from the aircraft industry. These are massive tools generally outside the hobby type user. I don't think you could run this in your garage at home and not have your neighbors coming out with pitchforks and torches to kill the monster. These are heavy duty industrial tools and are as scarce as moon rocks.
The simplicity of the helve hammer immediately appealed to me and my sense of design. Its just like hammering with a normal hammer but without the bursitis and sweat. I was interested in compound metalshaping but not all the heavy hand hammering physics lessons. This picture of a big Bradley forging helve is an example of a hot working helve hammer.
After seeing what was possible and being highly motivated after my trip back east I started my helve project in earnest.
An early design study. At this point I was thinking along the lines of a counterbalanced mass parallel action hammer. Not a true helve but similar.
This is a scan from one of my design notebooks. This is starting to show the final layout and some of the major design elements of the helve hammer. Note the curved arm on this study. My thinking on that was I might need additional clearance under the arm for deeply formed shapes. As it turned out I abandoned that idea when I looked at finding a chunk of quality hardwood big enough to cut that out of.
Another early design sketch. Here I was still contemplating an air cylinder as my power source. This is pretty close to the final layout. The major point here is that the construction method for the signature piece of a helve has been decided. At this point Its important to mention that I switched to a CAD system to do a more detailed layout and start the real mechanical design work.
Stay tuned for the next installment.
Helve Hammer Part 2
Some of the major design considerations for the sheet metal helve hammer presented some interesting problems. After doing some research into available components and weighing those against my desired budget influenced the process greatly. One of the goals for the project was to end up with a good set of plans and instructions that any decent mechanic with a few basic machine tools could put together themselves with some creative scrounging and an application of elbow grease.
The first big decision that affected many parts of the final design was the primary power source. In my survey of existing similar equipment there are quite a few examples of pneumatic cylinder driven forging hammers which I considered in detail. As a general rule compressed air is pretty inefficient for primary power sources. It has its place for many industrial applications but I discarded it for the helve hammer pretty quickly. First off you have to run an electric motor to compress the air. Most of the electrical energy used to compress the air is shed in heat as it being compressed. For the helve hammer I wanted around 200 hits per minute as the top end hammering rate. This would have required very large port high flow valves. When I spot checked a couple of proportional control valves the prices were out of my budget range for the project. The second reason for ditching the pneumatics was the need for throttling the rate, and force of the hammer blows.
Many of the industrial power hammers have electric motors connected via a clutch mechanism to the hammer mass. This solves a few problems right away. Switching to an electric motor is better for efficiency and they are readily available mass produced and cheap. I went to one of my favorite industrial recyclers and found a few motors that would work. For the desired range of hits per minute it called for a speed reduction from the standard 1800 rpm motor speed. I lucked out and found a motor gearbox assembly that was about right. It had the maximum horsepower and size that a decent 110V circuit would provide. Running on 110vac was also one of my desired criteria for the helve project.
The next stumbling block was the mechanical clutch. You would think there was a small simple mechanical clutch available for this kind of application but I found out that this wasn't a typical application and the available configurations were either too bulky and overkill or way too expensive. Its not for lack of examples. There are many of these things in equipment we use often but it seemed that most of these are purpose designed for the products we see them on. I figured if they design their own I guess I can too.
Luckily I have worked on enough motorcycles and have a good understanding of what was needed in a clutch for the helve hammer. The engineering company that I was working for at the time had used several overload protection devices to protect some mechanical cutting equipment from damage due to product jamming of the machine. Usually these are static devices that stay locked up but release when there is an overload condition. When they slip they behave just like a dry clutch but with less noise than a Ducati. When the load returns to normal they go back to driving without any input from the operator. This type is simple for applications where there is no synchronization of the drive system.
You can see the friction discs of the clutch in this picture. They are normally set and forget type clutches with a belleville spring maintaining the driving pressure to the sprocket. You just turn the machine on and keep tightening the clutch till the machine does what you want under normal loads. I just kind of inverted how they are normally used. If you leave it un-clamped when you don't need power and clamp it when you do then it works for the helve hammer. These devices are relatively inexpensive and dog simple.
Here is a shot of the electronic layout of the helve clutch assembly. The OSD (overload safety device) is in the center of this cross section of the clutch assembly. The actuator or throwout arm as the automotive guys would call it is on the right side of the drawing. Working out the actuation forces for the clutch was fun. I needed to start with some force that was reasonable and fairly accurate for actuation. This is a machine that is crying for a foot pedal to control the speed and force of the blows. So I started there with the foot actuation force. I have some human factors engineering books that tell you all kinds of fascinating things about humans and the kinds of knobs, levers and pedals they prefer and are optimal and ergonomic. I wanted a force less than the clutch actuation force for a car and more that an accelerator pedal was okay. The way I determined the force was by stepping on the bathroom scale a bunch of times and getting a number to calculate with and force that my foot and ankle were happy with.
This force drove the design of the foot pedal length and travel as well as the length of the actuation arm for the clutch. As you can see the pedal is connected via a cable to the actuation arm. Its an emergency brake cable for a Ford truck. Once again cheap and mass produced and already engineered by a army of engineers at Ford that want to keep their jobs. Good enough for my project.
In this picture you can see the actuation arm and the clutch in their respective positions. The drive system just sits there and idles once you turn it on. When you step down on the foot pedal the clutch pack compresses and transmits power from the motor to the eccentric on the left of the picture. I chose a v-belt because of simplicity and cost. It also gave me a little more pulley thickness to work with in the clutch assembly for a bearing when the hammer is idling. The clutch works better than expected. It can deliver a single hit or up to 240 hits per minute that will move steel sheet metal easily.
Next installment is the power recovery system of the helve hammer.
Helve Hammer Power Cycle
The mechanical helve hammer uses an eccentric actuated crank to raise and lower the Helve beam through an adjustable connecting linkage. As with any eccentric system the velocity varies with the rotational position. In a given full stroke the eccentric rotation passes through several important points.
If we divide one full revolution of the eccentric into four equal parts or quadrants we can look at the importance of each position. The first position we care about is what is called “Top dead center”or TDC for combustion engine shorthand. Top dead center is the position in the case of the helve hammer that raises the helve beam to its maximum height over the workpiece as shown in the picture above. The next position is 180 degrees opposite from TDC and is called “Bottom dead center” or BDC This is the lowermost position that the eccentric travels.In this position the hammer head is in contact with the workpiece or your soon to be tenderized fingers if your not paying attention.
These two positions represent the points at which the eccentric reverses its direction, and most importantly the eccentric velocity is zero. Any eccentric hammer system, whether it be Helve, Yoder, or Pullmax can be compared to a sine wave pattern.
Starting at zero we trace along the curve and at the peak of the curve we find the point TDC. Following the curve all the way to the bottom we then come to the point BDC. On the eccentric mechanism this represents 180 degrees (270-90) of eccentric rotation. The curve on this graph show one full cycle, or 360 degrees of eccentric rotation. As I stated the eccentric velocity is zero at the extreme ends of travel. If the Helve hammer mechanism were rigidly connected to the eccentric motion it would produce a squeezing action as opposed to a hammering at the ends of the stroke. This is fine for things like press brakes and punch presses where we want to produce a large pressure or force but not for power hammers that operate by impacting the work to move material.
For power hammer design the point we care the most about is the point of maximum velocity. That point is halfway between TDC and BDC. This point is both 90 degrees from TDC and BDC. At this point the eccentric shown in the picture is neither speeding up or slowing down it is actually traveling at the same angular velocity as the motor for just a split second.
Power hammers differ from other eccentric or reciprocating systems in that they have an added spring in which to store some of the inertial energy of the hammer head and impact mass generated during the eccentric cycle. The spring compresses on the upstroke, and extends on the down stroke. For the helve hammer I designed and built the flat spring made from heat treated 17-4 PH stainless steel.
Helve hammers have an swinging arm and a hammer head which have a combined mass that is unique to each hammer. This mass rotated by the eccentric has an inertia. The purpose of the spring is to store some of that inertia on the upstroke and release it on the down stroke. So what is really happening is the mass of the hammerhead and beam is traveling slightly behind the eccentric. As the eccentric is passing through that point at BDC where the velocity is zero the hammer head has been accelerated to the maximum velocity and flung past that point of zero velocity (BDC) thereby delivering a impact blow and releasing the stored energy in the spring instead of giving a harsh squeeze.
The spring that stores the energy needs to have the proper rate for the inertial mass of the hammer. If it is too weak the hammer will flail and miss hit dissipating much of the potential hammering energy in a silly looking dance. If the spring is too stiff it will not release the stored energy at the correct rate, squandering it for some meaningful work. When the spring rate is correct the hammer will hit harder and harder as the speed of the eccentric increases, releasing the maximum stored energy and transmitting it to the work. This tuning is important because this is how the force of the hammer blow is regulated. By varying the speed with the clutch the operator controls the force of the blows. The ability to slip the clutch and control the speed between the motor and the eccentric is essential to a successful power hammer design.
These spring rates can be calculated, (tediously) but I recommend building in some adjustability to the spring mechanism that allows some change of the rate of the spring. Power hammer springs show up in many forms. flat, leaf, coil, and elastomeric just to name a few.
There are many variables that effect how a power hammer hits. System mass, storage spring rate, rebound, and eccentric offset all play a part in the hammer system. It is hard to change any one the variables without effecting the others. My advice to anyone who would like to build a power hammer is to engineer in a little adjustability and fudge factor into all of these areas to allow for some tune-ability and to address tooling mass changes or the different rebound characteristics of various anvils and the different materials being worked.
I would like to caution builders to use common sense and good design practice when constructing and using a power hammer. These are serious metalworking tools and could really injure the unwary and cause life changing injuries if not treated with respect. Imagine trying to pick your nose with your thumb or use your smart phone with a pirate hook instead of a meat hand.
These machines smash and mangle metal without a second thought. In all pursuits if you hurt yourself take responsibility for your actions. The facts are this, you will get pinched, cut and crunched doing metalwork. If you put your finger in the mouth of a mean dog and it bites down, can you blame the dog for being a dog? Treat all machinery like a mean dog that thinks your body parts are all made from solid bacon.
Tom Lipton
No comments:
Post a Comment